Table Of Content
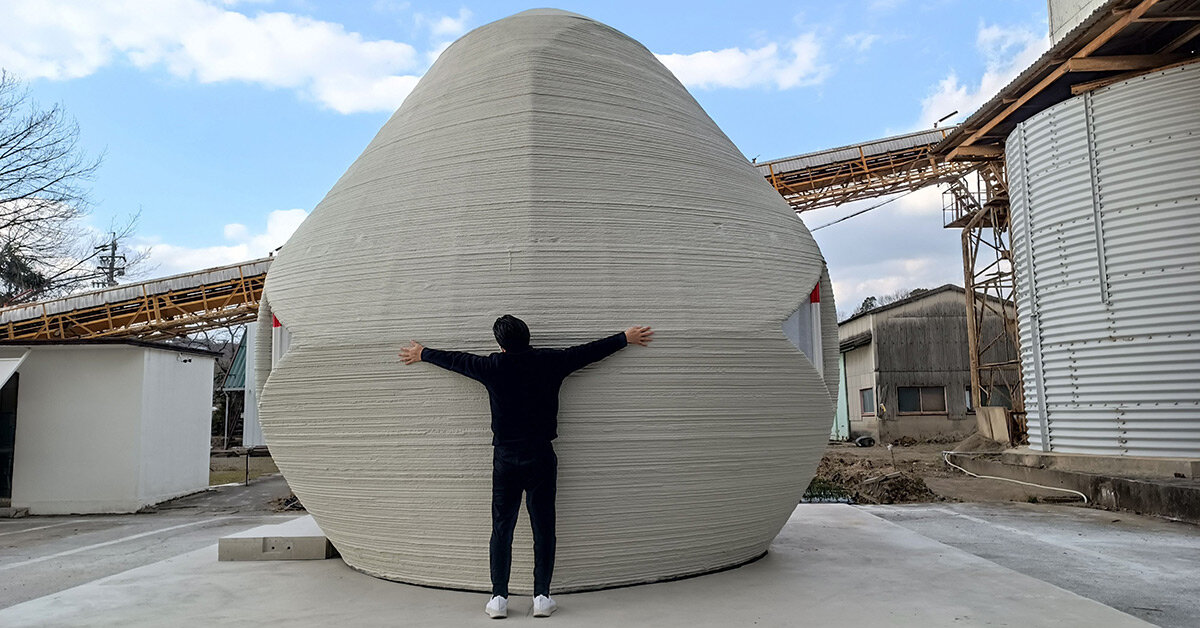
Made out of a steel, quad-truss framework — the kind you’d see as part of a concert stage — these industrial-grade 3D printers form a sort of hollow cube. On top, a robotic arm zips along a track, following pre-programmed instructions being read from the blueprint. Nowadays, industrial-sized 3D printers have made it possible to print an entire house in less than 24 hours. This two-bedroom 3D printed house floorplan embraces simplicity in the most straightforward manner. With two quaint bedrooms and a single bathroom, this floorplan is just right for a couple or small family that doesn’t need a lot of extra room but appreciates individual sleeping areas. This three-bedroom home has plenty of space for living, lounging, and storage.
Which is better, OSB or plywood for roofs, walls and floors?
3D-printed homes are created using large concrete 3D printers, and they are typically more affordable than traditionally constructed homes — plus, they’re also built in a sustainable fashion. As companies like Icon continue pushing the envelope on technology to unite 3D-printed forms with typical architectural elements, residents of 3D-printed homes find them remarkably comfortable. Village, a 51-acre development aiming to provide homes for unhoused people in Austin, has been pleased by how livable and cozy he’s found his 400-square-foot home. "There are no sharp corners in the house, and the roundness is embracing," he says. "It feels warm, secure, and comforting inside—it’s like I’m being hugged by my house." NASA has designed, with the company ICON, a 170 m2 3D printed habitat in order to simulate a mission to the Moon (Project Olympus), where buildings could be constructed using resources found on the Moon.
Autodesk metal construction printer
Our dedication lies in revitalizing smaller communities, offering them sustainable and affordable living spaces. By harnessing the power of innovation, we are transforming economically distressed and under-served communities, providing them with the infrastructure they need to flourish. Through state-of-the-art 3D printing technology, we’re pioneering innovative, stronger, faster and more cost-effective building solutions that are environmentally responsible. However, this is America, so it’s not like people built this thing just to help the unhoused. UMaine researchers received funding from the Army Corps of Engineers, the Department of Defense and the Department of Energy. These governmental institutions are going to want a return on their investment, so the printer will also likely be used to whip up lightweight rapidly deployable vessels, like submarines and other maritime vehicles.
Infrastructure Construction
The 3D printing process is usually paused to manually settle plumbing, wiring, and rebars. To provide a complete overview of the construction 3D printer market, we have listed 12 house 3D printing solutions. Some of them are 3D printers available for sale, while some are still at the start-up prototype stage or are external construction 3D printing services. Only the frame and walls of the house are built; other elements, such as windows, electricity, or plumbing, need to be installed separately. But concrete 3D printers can also be used to print bridges, benches, or simply outdoor decorations. Just as with traditionally constructed homes, 3D-printed homes are available at a variety of price points — though they are generally more affordable.
Differences between 3D printed houses and traditional houses
There are also companies that will take your building plans and create walls to match that can be delivered and assembled, that can be a great option as it is often cheaper as there is less material waste. And, you’re not leaving your wood frame exposed out in the rain for weeks or months to get saturated and warped. So we call for caution when it comes to believing everything you might find online about 3D printed homes being "the" solution to the challenges facing the North American construction industry.
Why did Iowa demolish its first 3D printed house? - 3d adept media
Why did Iowa demolish its first 3D printed house?.
Posted: Tue, 28 Nov 2023 08:00:00 GMT [source]
Material Options For 3D Tiny Houses
The FoF 1.0 has a sibling printer on the UMaine campus, which was the previous record holder for the world’s largest 3D printer. It’s already been used to manufacture a 600-square-foot, single-family home made of wood fiber and bioresin materials. Luckily, the two models are housed in the same location and can work on different aspects of the same projects simultaneously. Concrete 3D printing saves time, uses less material, and requires less manual labor. Even 3D printed houses have a rougher exterior, post-processing is an option just as it is for regular 3D printed objects.
Thermoplastic polymers are extruded from a printer dubbed the "Factory of the Future 1.0," said Habib Dagher, director of UMaine's Advanced Structures & Composite Center, where both of the current printers are located. It combines robotics operations with new sensors, high-performance computing and artificial intelligence, Dagher said. Thermoplastic polymers are extruded from a printer dubbed the “Factory of the Future 1.0,” said Habib Dagher, director of UMaine’s Advanced Structures & Composite Center, where both of the current printers are located. Prices vary greatly according to the material being used and the size of the home to be 3D printed.
50 Cool Things to 3D Print for April 2024 - All3DP
50 Cool Things to 3D Print for April 2024.
Posted: Mon, 01 Apr 2024 07:00:00 GMT [source]
"ICON claimed that its technology "could" 3D print the building in 24 hours, but provided no documentation to prove it" (COBOD). For the time being, 3D constructions are mainly made of mortar-concrete or plastic, materials that have a heavy environmental impact. In terms of costs, several articles consulted speak of a 50% cost saving for the "house". It would seem that the savings are only in the wall structure, since only the walls are printed (and that it would be more like 10-20%, due to the cost of labor, which is less on a printed structure). The first 3D house, built by the international organization Habitat for Humanity in Virginia, while it took only 28 hours to print the concrete walls, the construction site to complete the house took as long as a traditional house.
House 3D printing technology
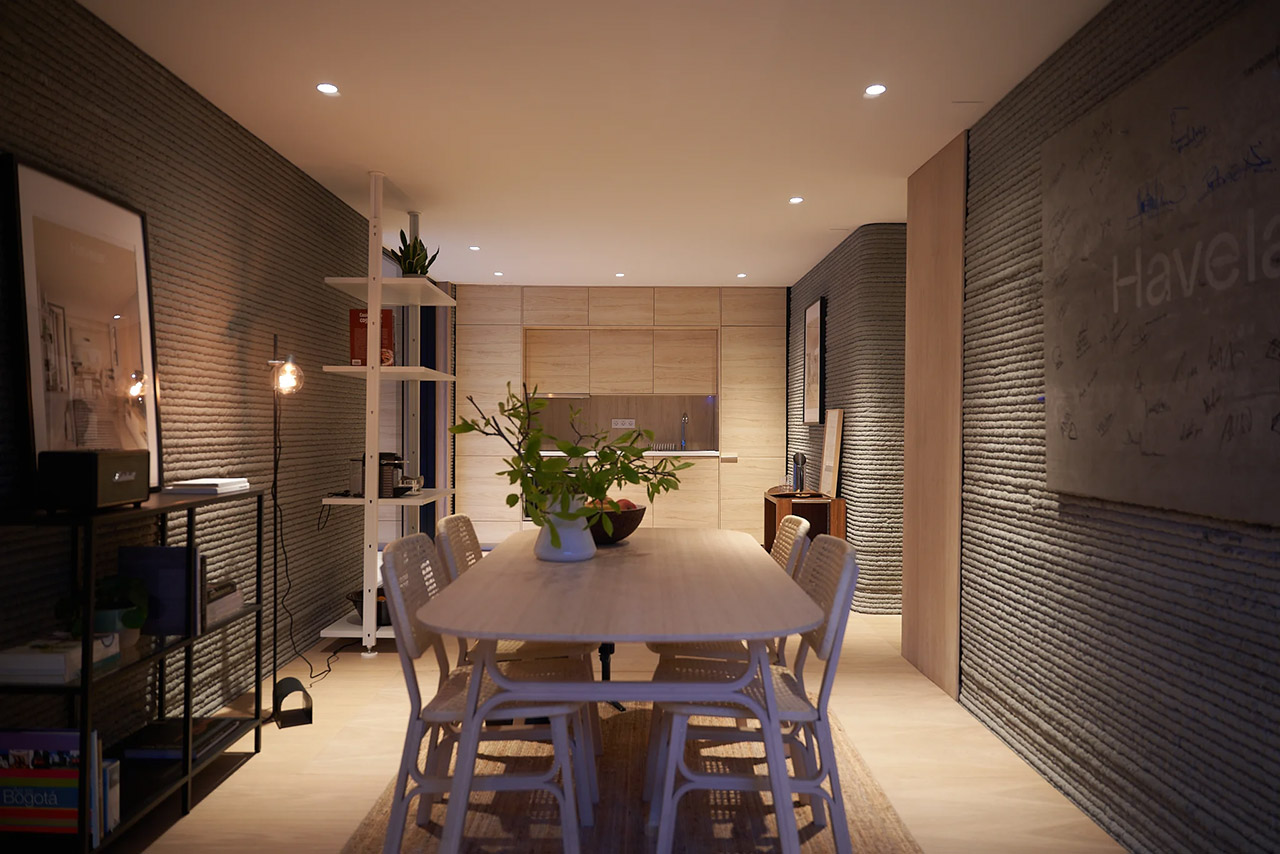
This is simply not plausible for traditional builds as they are more restricted by the shape of bricks, whereas 3D housebuilding can create curved shapes without issue. This offers potential for more compelling designs, as well as creating custom houses to suit disabled people. ICON, a 3D-printing construction company, said it could produce a 600 to 800-square-foot, economy-sized building for as low as $4,000 in 24 hours, as reported by Business Insider.
3D homes are unimaginably cheaper to construct, and it’s possible to build a complete house in 24 hours. The capabilities of the ARCS line of concrete 3D printers become immediately evident once stepping foot inside of an SQ4D printed home. Concrete mixtures specifically formulated for 3D printing enable the printers to layer the material effectively. Another material gaining popularity is bioplastics, derived from renewable sources such as cornstarch or algae. In what is set to become the “largest-scale development of 3D-printed homes globally,” Danish architecture studio BIG and American 3D-printing firm ICON have successfully completed a full-sized model home. Bologna-based architecture studio Mario Cucinella Architects and 3D-printing specialists WASP collaborated to create a 60-square meter low-carbon housing prototype named Tecla – a combination of the words technology and clay.
Over in Wallenhausen, Germany, German-based construction company PERI Group started construction on a 3D printed three-story multi-family apartment building, following the success of the two-story home they printed earlier that year. This is in conjunction with their new East 17th Street initiative, a project that hopes to use this innovative technology to build a small community of 3D printed homes in the growing area of East Austin. Joining forces this time with developer 3Strands, ICON has used its Vulcan technology to construct four multi-story buildings in East Austin ranging from 1,000 to 2,000 square feet, featuring modern open plans and timeless interiors. For the full story covering the world’s largest 3D printed building, click here. Some real estate marketplaces like Zillow, or some homeownership assistance programs like Habitat for Humanity, can sell 3D-printed houses. Much like your desk-side inkjet printer, the mixture is then heated during a thermal extraction process.
They share a color palette of green, white and terracotta and have all been sold. Three-dimensional-printed houses are structures that are built layer by layer using an industrial-grade, 3D-printing technology. This method of additive manufacturing is also known as construction 3D printing.
Paste-type material, in this case, concrete or earth materials, is pushed through a nozzle in layers to print buildings in 3D. These four Austin, Texas properties by construction 3D-printing company ICON feature open-floor plans, minimal architectural aesthetics and private yards. Varying in size, these residences feature two to four bedrooms and range from 1,000 to 2,000-square-foot homes. Each ground floor level is built with a proprietary cement-based material, dubbed “Lavacrete,” to last longer than traditional construction materials, according to the company’s website. The second story incorporates old-school methods, and is constructed out of black metal cladding and rich-colored timber.
For a select group of global citizens who’ve found themselves living in a 3D-printed homes, while the reality may not be quite as glamorous as House Zero, it’s nevertheless been surprisingly comfortable. Inside, House Zero looks and feels like a traditional home, but with undulating 3D-printed exterior walls that offer an element of texture and movement to interior spaces. However, it will take many years before it becomes a normalized building method. The team starts by adding dry Lavacrete (a special form of concrete), water and additives into a portable mixing machine known as Magma. Once the material is properly mixed and ready to go, Magma pumps it into the Vulcan for printing.
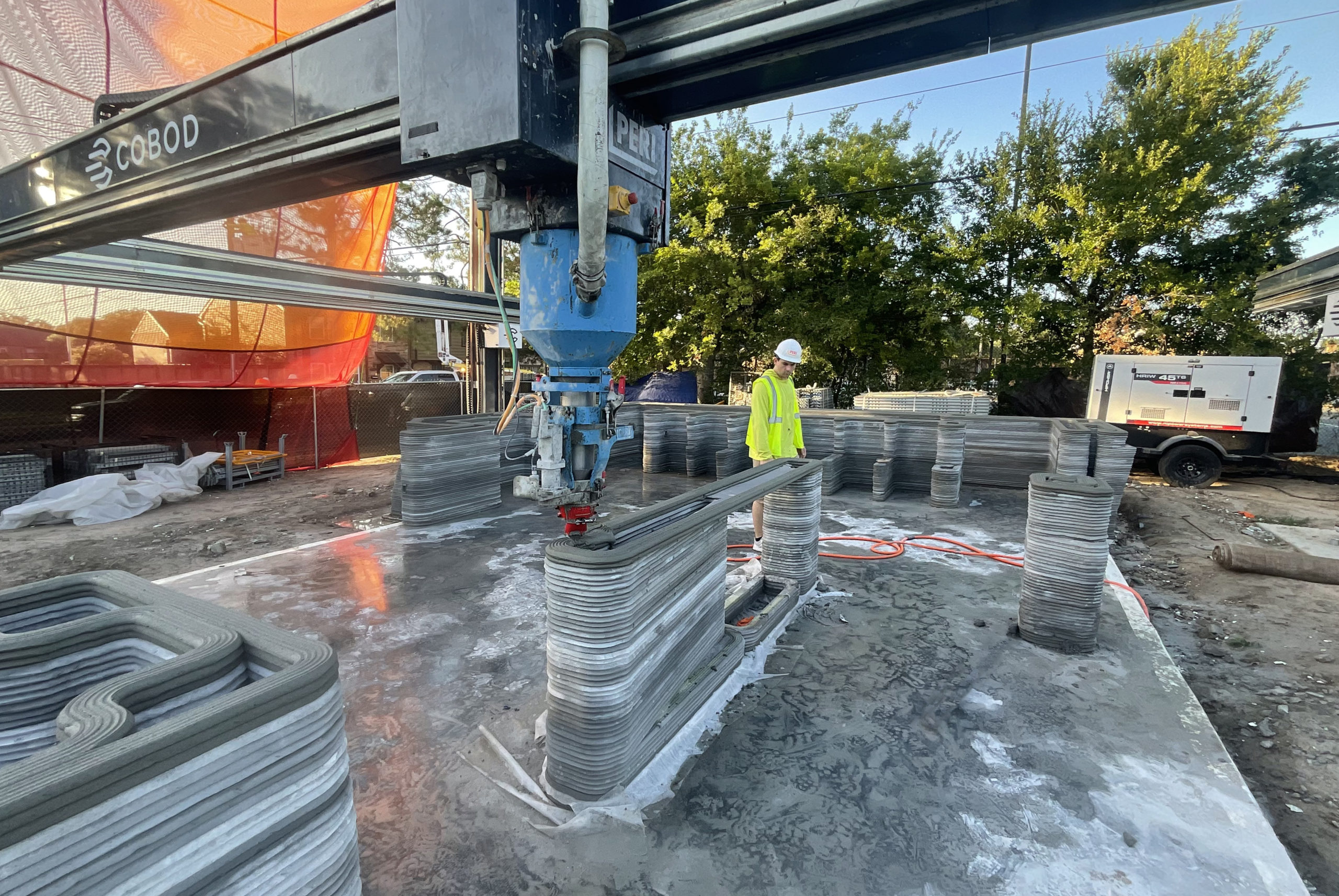
Simply put, three-dimensional shapes are at first designed through a computer-controlled process without the use of formwork. It – minimizes material use, uses natural, organic or recycled materials, generates less waste, decreases transportation needs as well as reduces carbon footprint. Unlike other 3D printing outfits, Mighty Buildings uses a resonated stone composite called Light Stone Material in their printers, which hardens when exposed to UV light and is highly durable and thermally stable. "I was worried," admits Phoenix, Arizona, resident Marcus Shivers about his initial reaction to hearing he could be moving into a 3D-printed home. "It looked like a nice house in the mock-ups, but my main concern was that the technology was new—I wondered who would actually know how to work on the house if something went wrong." The company is also working towards more complex architectural capabilities like geometric designs, patterned walls and domes.
No comments:
Post a Comment